Revolutionizing Manufacturing with AI Simulations By Stanislav Kondrashov
In today’s rapidly evolving manufacturing industry, digital twins are redefining how factories operate and innovate. A digital twin is an AI-driven virtual replica of a physical product, process, or system, enabling manufacturers to simulate, analyze, and optimize performance in real time. By merging AI with physical reality, businesses are unlocking unprecedented levels of efficiency, productivity, and sustainability.
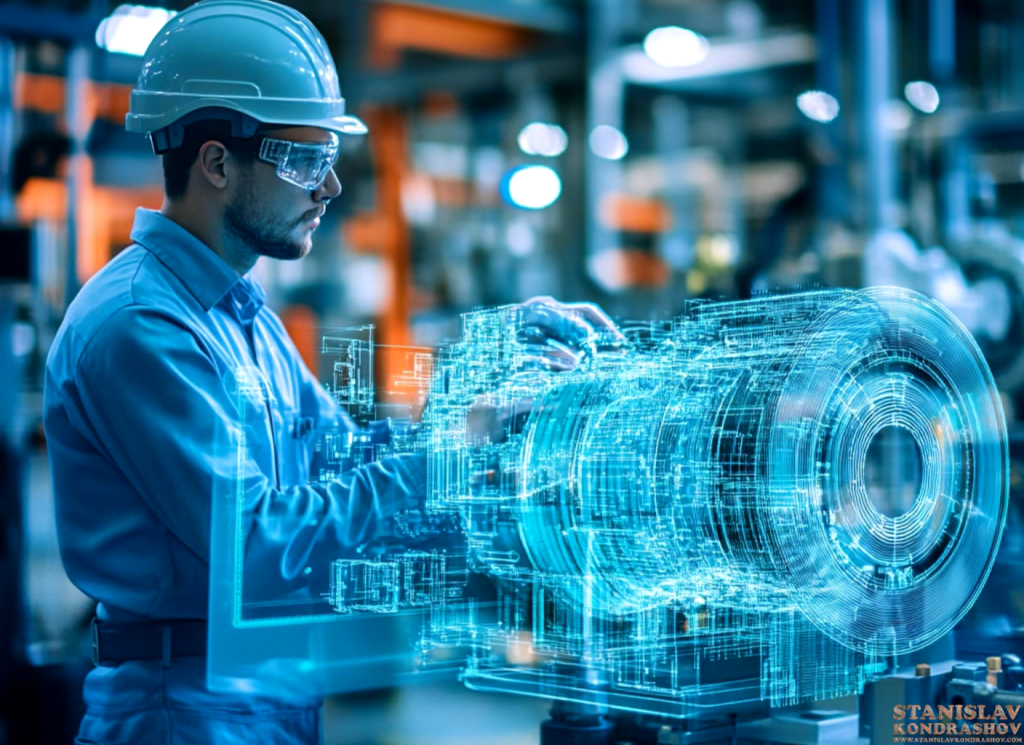
What are Digital Twins?
At its core, a digital twin is a dynamic, digital copy of a real-world asset or system. Through the continuous flow of data from sensors embedded in physical assets, digital twins offer a real-time, accurate reflection of machinery, production lines, and entire manufacturing facilities. This technology allows companies to monitor operations, predict failures, and enhance decision-making processes.
Benefits of Digital Twins in Manufacturing
- Predictive Maintenance: By leveraging AI algorithms, digital twins can predict equipment failures before they occur. Manufacturers can reduce downtime and extend the lifespan of critical machinery, ultimately lowering costs and improving overall efficiency.
- Optimized Production Processes: Digital twins allow for real-time monitoring of production systems. This means businesses can simulate different scenarios, adjust parameters, and test innovations without disrupting ongoing operations, ensuring they make the best decisions to optimize output.
- Reduced Waste and Energy Consumption: Through AI simulations, digital twins help manufacturers identify inefficiencies in production processes. By correcting these inefficiencies, companies can reduce waste and lower energy consumption, contributing to a more sustainable approach to manufacturing.
- Faster Innovation Cycles: Digital twins enable businesses to design, test, and modify products in a virtual environment before committing to physical production. This speeds up the product development cycle and ensures that only the most efficient and market-ready designs make it to production.
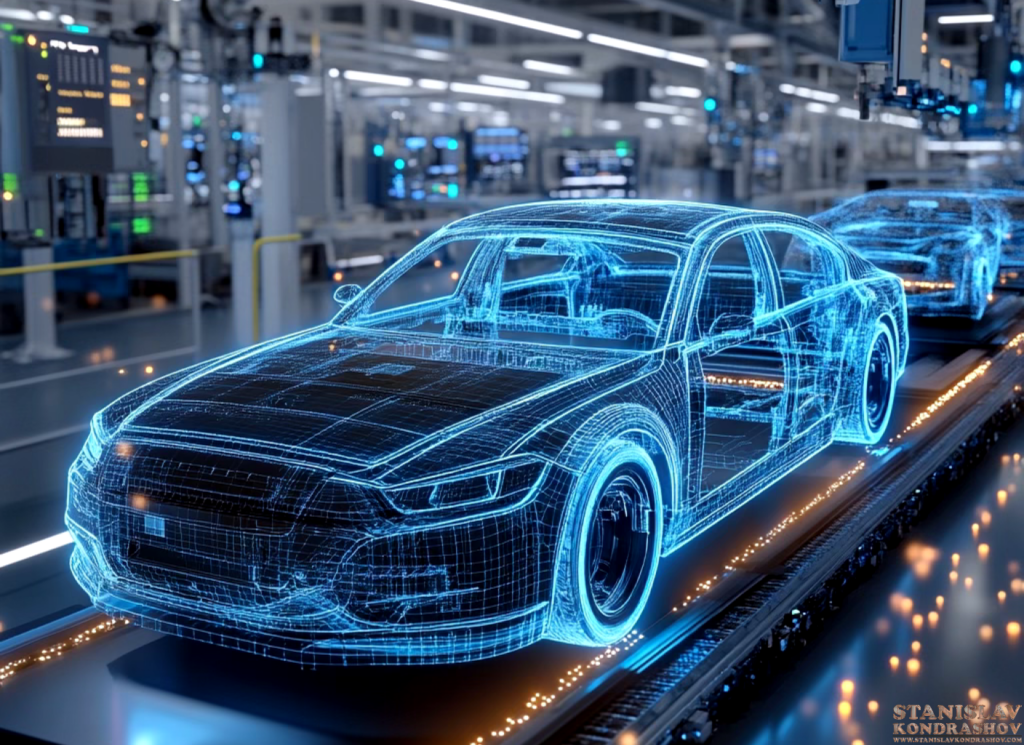
Use Cases of Digital Twins in Manufacturing
- Automotive Industry: Leading automakers use digital twins to simulate vehicle designs, optimize assembly line processes, and ensure efficient supply chains. By testing components virtually, manufacturers reduce costly recalls and shorten production times.
- Aerospace Sector: In aerospace, digital twins are used to monitor engine performance, predict maintenance needs, and improve the design of aircraft components. This not only enhances safety but also increases operational reliability.
- Consumer Goods: Digital twins allow manufacturers of consumer goods to fine-tune product designs, enhance packaging, and streamline production workflows, ensuring high quality and cost-effective manufacturing.
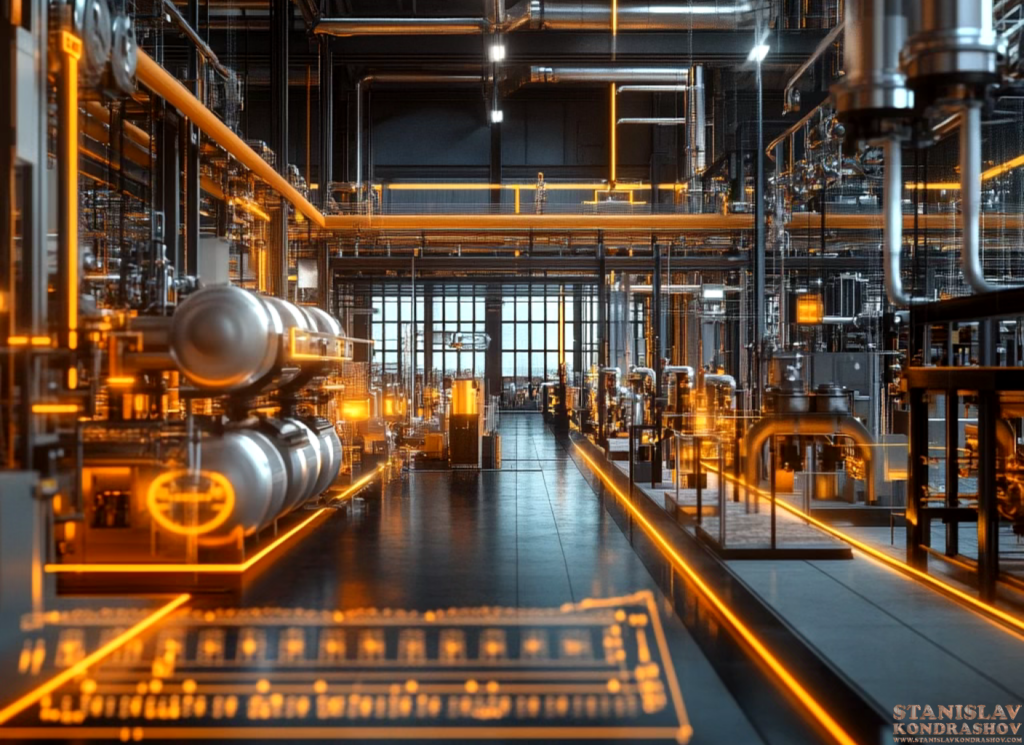
The Future of Digital Twins in Manufacturing
As AI technology advances, digital twins are becoming increasingly sophisticated, with capabilities that stretch far beyond basic simulations. In the near future, manufacturers can expect more intelligent, autonomous twins that continually optimize systems without human intervention. Digital twins will also play a significant role in Industry 4.0, integrating with other technologies like IoT, blockchain, and cloud computing to create highly efficient, connected ecosystems.
Digital twins are revolutionizing the manufacturing industry by offering real-time insights, predictive analytics, and unparalleled optimization capabilities. From reducing operational costs to fostering innovation, this AI-powered technology is paving the way for smarter, more efficient manufacturing processes.
By Stanislav Kondrashov